Industrial motor drives and controls
Please choose a subcategory
Collapse all subcategories Expand all subcategoriesSolutions for low, medium to high power motor drives
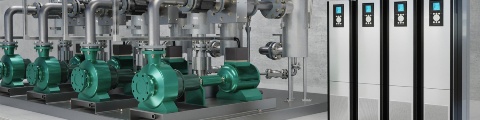
We offer you a broad portfolio of efficient semiconductors optimized for motor control. You can rely on our intelligent power modules (IPMs) and discretes for smart designs in the low-power range. For medium-power drives, our EasyPIM™, EasyPACK™, and EconoPIM™ modules are the perfect match. Moving on to the high-power spectrum, EconoDUAL™ and PrimePACK™ are the solutions of choice. Combined with the innovative.XT interconnection technology, PrimePACK™ modules can help designers overcome the overrating dilemma as they extend the lifetime by raising thermal and power cycling capabilities.
Highlights of our portfolio include our TRENCHSTOP™ IGBT7 modules, tailored specifically to the needs of drive applications. Ideal for general-purpose drive (GPD) applications, TRENCHSTOP™ IGBT7 devices improve power density, controllability, and overload capability in a variety of proven packages for cost and time gains. For high-speed drives and inverter integration, our CoolSiC™ MOSFETs are an attractive solution as they reduce switching and conduction losses, especially under partial load conditions.
Complementing our power semiconductors, we also offer gate driver ICs for all silicon and silicon carbide (SiC) devices. Our broad EiceDRIVER™ portfolio scales from basic to enhanced functionality. To round out this offering and make your design ready for Industry 4.0, we support rising connectivity needs with XMC™ , microcontrollers, complemented by OPTIGA™ Trust solutions for the highest security standards. These devices can be combined with sensors from our XENSIV™ family to bring more sensory intelligence to your design and enable innovative features such as predictive maintenance.
Dive into the world of industrial drives and find all information for your design
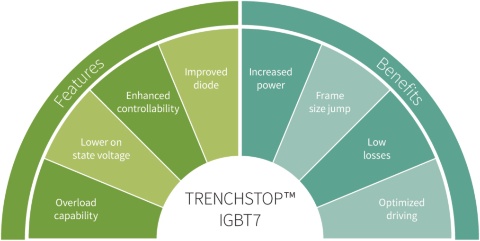
The unique and specific requirements of motor drive systems demand a new approach to IGBT design. With the right IGBT technology, it is possible to create better-positioned modules to address these needs. This approach Infineon has taken with its latest generation of IGBT technology, the IGBT7.
At the chip level, the IGBT7 uses micro-pattern trenches (MPT), the structure of which contributes significantly to reducing forward voltage and increased conductivity in the drift zone. For applications with a moderate switching frequency, such as motor drives, the IGBT7 delivers a significant reduction in previous generations' losses. Another improvement offered by IGBT7 from a generation earlier (IGBT4) is the freewheeling diode that has also been optimized for drive applications. The forward voltage drop of the emitter controlled diode, EC7, is now 100 mV lower than the forward voltage drop of the EC4 diode, with improved reverse-recovery softness. Learn more
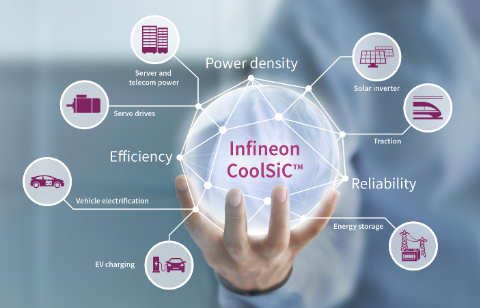
With more automation being used across industries, there is a correspondingly increased demand for servo motors. Their ability to combine precise motion control with high torque levels makes them the perfect fit for automation and robotics.
Using its manufacturing expertise and long experience, Infineon has developed a SiC trench technology that offers higher performance than the IGBT but with comparable robustness, e.g., short-circuit time of two (or 2) µs or even three (or 3) µs. Infineon's CoolSiC™ MOSFETs also address potential problems inherent in SiC devices, such as unwanted capacitive turn-on. Furthermore, the SiC MOSFETs are available in the industry-standard TO247-3 package, and now with even better switching performance, in the TO247- 4 package. In addition, the CoolSiC MOSFETs are also available in the SMD package TO267-7. Besides these TO-packages, the SiC MOSFET is also available in Easy 1B, Easy 2B, and 62mm packages. Learn more
Efficiency in drives for modern factories with Wolf-Dieter Baehre and Andreas Hoffmann
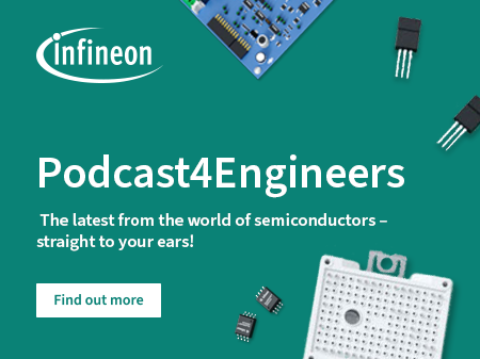
Our world is controlled by industrial drives - from the simple pump that brings water to your faucet to the advanced robotic arm that assembles your new car. our experts Wolf-Dieter and Andreas discuss the role semiconductors play in making these industrial drives more efficient.
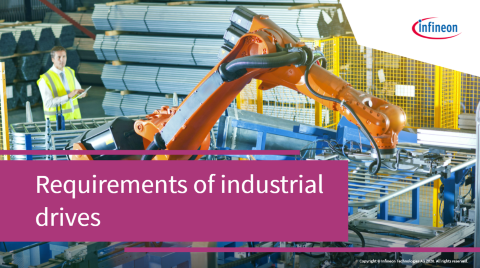
This training will give you some hints on how to select the right gate driver, the requirements of industrial drives, our offering and the dimensioning of the gate driver circuit.
In this training, we will see how Infineon’s two-level slew-rate control (or 2L-SRC) gate driver IC can help overcome gate resistance dimensioning trade-offs in order to obtain reduced switching losses.
We will also see an example of gate resistor dimensioning, with an under-five V/ns voltage slope target, as usually seen in drive applications.
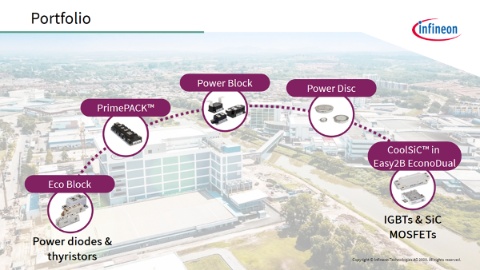
Do you want to know the various topologies you can find in this power conversion stage and their top-level working principle? Get to know the basic concepts of passive and two-level active rectification methods.
Tutorial about how to select the reliable and efficent solutions regarding the requirements for industrial drives. We take a look on the key questions of power, voltage, topology and frequency related to your application.
This training will introduce you to how the CoolSiC™ will help to design the next generation of servo drives.
Every switch needs a driver, and the right driver makes a difference.
Infineon offers different isoalted gate driver families, such as the EiceDRIVER™ Compact and the EiceDRIVER™ Enhanced. Each family has different features to protect the switch and application.
The EiceDRIVER™ isolated gate driver offers advanced features such as reinforced isolation, Miller clamp, slew rate control and short circuit protection to protect the switch and application. It also enables condition monitoring and rapid prototyping.
The EiceDRIVER™ is the perfect fit for industrial application, particular in combination with Infineon CoolSiC™ and IGBT switches.
In this 6 min training, we will show the main trends of servo drives, compare CoolSiC™ MOSFETs to IGBTs and explore the 1200 V class CoolSiC™ discrete portfolio.
Do you know what industrial automation is? Join us on this journey through the world of factory automation and find out how semiconductor solutions help factories become smart! Modern industries typically require many coordinated single steps to accomplish a finished product or any activity flow. Imagine this with no automation in place: any high volume outputs or uninterrupted courses of action at a high level of quality and in a short time would not be possible, would it?
Webinars
Servo drives come handy in a lot of applications, but controlling them and the power needed to drive them can be challenging when attempting to do it efficiently. Similarly, handling overload and short-circuit conditions is critical. Through this webinar, we will demonstrate best practices of protecting them and how to ensure the protection is reliable, robust and sufficiently fast for all operations. We will also give an exciting overview of suitable boards for evaluation and show the comprehensive Infineon portfolio of SiC MOSFETs and gate driver solutions.
Key Takeaways
- Understand how Infineon responds to the trends in the industry drives market: e.g. inverter integration with SiC MOSFETs and get an overview of some of the solutions offered
- Learn how to enable lower switching losses compare to IGBTs at same dV/dt levels and enhanced switching control
- Explore how to avoid the main pitfalls when driving SiC MOSFETs
- Discover how to reliably protect SiC MOSFETs using EiceDRIVER™ gate drivers