Vacuum cleaner
Rising electricity costs, stricter government regulations and greater consumer expectations: these factors are driving manufacturers to design more energy efficient, quieter and compacter vacuum cleaners and vacuum robots, with better value-for-money. To stay competitive, manufacturers must increase motor power to improve suction, use higher speed motors and find a way to differentiate their vacuum cleaning system. Likewise, better energy efficiency is attained by reducing power consumption. In comparison to their predecessors, today’s vacuum cleaners are compacter, lighter and significantly longer in lifetime – all aspects with great consumer appeal.
Vacuum cleaner system diagram
Vacuum cleaner technology from Infineon
To help you overcome these vacuum cleaning system challenges, Infineon offers a comprehensive portfolio of discrete IGBTs, such as the RC-Drives (RC-D) and RC-Drives Fast (RC-DF), discrete MOSFETs and IPMs. Outstanding performance efficiency, small component size and our wide product range allow you to design a compact, highly integrated and more powerful vacuum cleaner system at a lower price. All factors that significantly contribute to a product’s success on today’s market. Also, our wide range of complementary products – drivers, sensors and controllers – are ideal for all stages of vacuum cleaner power management.
Questions about your design? With years of vacuum cleaner technology experience, Infineon engineers are available to help optimize your system design and cost, expediting the time it takes to get the products to market. Expect more and get more when you select Infineon for vacuum cleaner applications.
Podcast4Engineers: Home Appliances
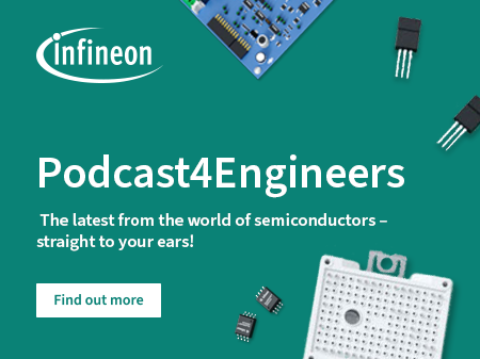
Smartification and electrification aren’t just limited to our smartphones and computers anymore; these trends are steadily making their way into our home appliances and the market is booming. But what technologies are driving home appliance innovation and how do semiconductors play a role?
Listen to our latest podcasts to learn more about home appliances and how Infineon technology is powering the smart home of tomorrow.
Whitepaper: The rise of the smart kitchen
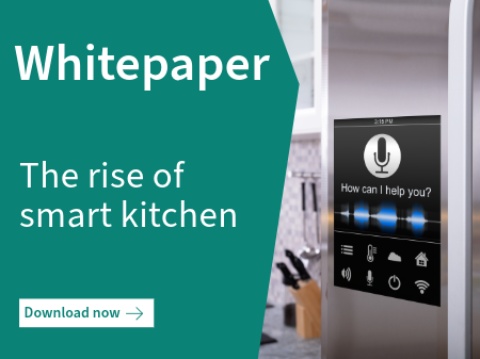
This whitepaper charts the rapid rise of the smart kitchen and looks at how advances in electronic solutions have resulted in a new generation of quieter and more energy-efficient appliances driven by intuitive sensor-based operation.
Webinar: System solutions for the smart home appliance era
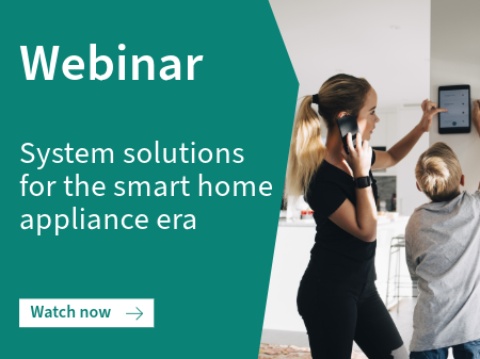
Modern home appliances are increasingly smart and connected, providing a seamless, remote user experience. Users control operation and receive live data from appliances, whether it's the contents of the refrigerator or information on the status of laundry. In turn, manufacturers can remotely analyze the device and suggest predictive maintenance to avoid costly repairs. This webinar will show you how Infineon's smartest power designs can help you achieve the highest efficiencies, smallest form factors and significantly improve your appliances' carbon footprint to make them smart, connected, and secured.
Whitepaper: Power device choices in the new small home appliance market
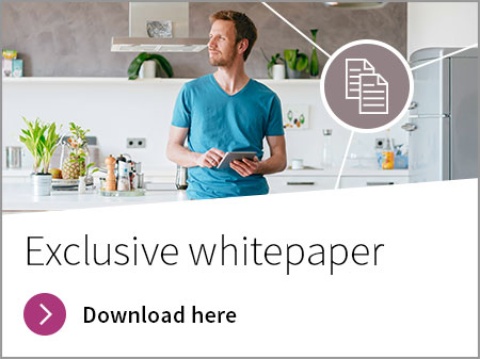
Dive deeper and discover more about the changing landscape of SHA market and enablement of electronic solutions in this free white paper.
Inductive Wireless Charging Up To 50 W: Powering Applications You May Not Have Thought About

As more and more portable electronics are looking for ingress-proof designs, inductive wireless charging seems to be the perfect solution for current as well as future market needs. Learn more about the key trends in wireless power transfer and how Infineon´s portfolio can be the best fit for a wide variety of emerging applications.
Webinars
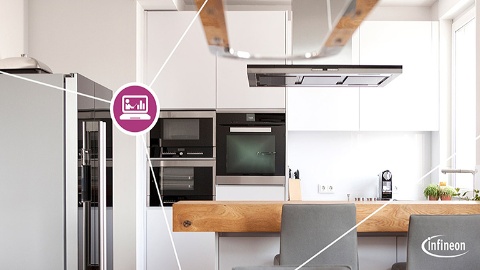
We review power devices enabling efficient designs, meeting energy regulations & enabling software-based smart functions.