Motor control and driver
Get your BLDC motor running with easy-to-implement reference designs and support tools for selecting the best-fit parts for your motor driver application.
As the need for energy-efficient motor control continues to expand, so does the requirement for the necessary resources and components from their respective supporting ecosystems.
As a semiconductor supplier with extensive system knowledge, Infineon focuses on developing affordable and energy-efficient motor control solutions that meet the highest safety standards. We support a comprehensive ecosystem including online simulation access, reference designs, evaluation boards, Arduino kits, our ModusToolbox™ embedded software development solution, and components that can seamlessly be reused across multiple projects to meet all kinds of design requirements. From individual components to fully integrated solutions, our products address the key considerations for modern motor control systems.
Moreover, considering the high CO2 emission reduction targets set in the industrial, consumer and automotive industries, Infineon's comprehensive range of semiconductor solutions continues to expand. From our OptiMOS™ MOSFETs, EiceDRIVER™ bridge drivers to MOTIX™ integrated bridges, we provide components optimized specifically for modern motor control systems, capable of satisfying requirements for the full spectrum of motors - brushed and brushless DC (BDC and BLDC), induction, permanent magnet synchronous (PMSM), servo, stepper, and switch reluctance motors.
This training provides you some hints on servo drives and their application in robotics.
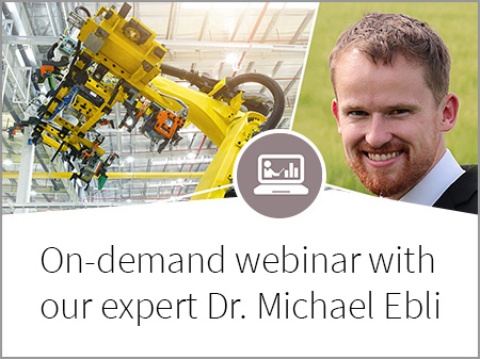
Silicon Carbide MOSFETs are a perfect match for servo drives? That’s right! This special #webinar reveals why compares performance levels of IGBTs versus SiC MOSFETs and explains the benefits of using Infineon’s.XT interconnection technology.
By taking this course you will learn about…
- the motor control and drive functional blocks
- Infineon offerings for these blocks
- the benefits of choosing Infineon solutions

This training will focus on some advanced topics for motor drives.